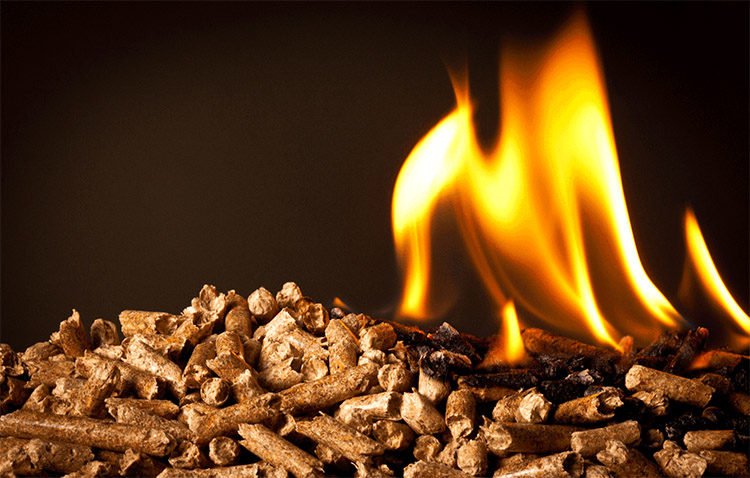
As the combustion performance is the main concern of the end users. Therefore, get the comprehensive information of different biomass pellets combustion properties is quite important for the biomass pellet plants to produce the suitable biomass pellets for proper markets. We have talked about the design of biomass pellet combustion property test in the last post. This time, we will analyze the combustion property of the eight kinds of biomass pellets based on the test result.
Biomass Pellet Ignition Property
According to the test of eight kinds of biomass pellets, the ignition property of biomass pellets is closely related to the volatile component and moisture content of the biomass pellets. Among all the biomass materials, larch maintains the highest volatile component, and lowest moisture content. Therefore, larch pellets has the shortest ignition time. On the contrary, cotton stalk holds the lowest volatile component and highest moisture content, which needs the longest ignition time. Biomass pellets ignition time is linear to the volatile components of the biomass pellets. The higher the volatile component is, the shorter ignition time the pellets need. This is because the volatile component of biomass pellet consists of several combustible gases, such as hydrogen, methane, unsaturated hydrocarbon and carbonic oxide. So when there are more volatile components in the biomass pellets, it is easier to ignite. The ignition time of biomass pellets has exponent relation to the moisture content of the biomass pellets. The higher the biomass pellets moisture content is, the longer ignition time the biomass pellets need. This is because the high moisture content of the biomass pellets will lengthen the drying time and lower the max combustion temperature, so the ignition time of the biomass pellets is longer, too. Also, we should know that when the moisture content over the certain value, the biomass pellets can not be ignited.
Biomass Pellet Combustion Property
The description of biomass pellet test presentation
After the observation, the combustion process of eight kinds of biomass pellets can be divided into four stages, the start-up, pre-run, operation stage and stop stage. When the start-up stage starts, the flue gas is white and consists of vapour, the blackness of the gas is high. When we have successfully ignited the pellets, the color of the flame is red, and the temperature is low and the blackness of gas is lighter. The gas is black or grey which caused by the lack of combustion air during the burning period. In the pre-run stage, the flame becomes orange, the temperature goes higher and the blackness of the gas is much lighter. During the operation stage, the fire flame becomes light yellow, the gas is light smoke. At the stop stage, the blackness of gas grows again, and the fire flame turns down.
CO emission during biomass pellet combustion
After the combustor starts, the CO content of the flue gas is increased till the peak value. When the combustion goes into the operation stage, the CO content goes down. The analysis shows that the combustion chamber maintains low temperature and the supply air rate is small but the feed quantity has reached the pre-set value in the start-up and pre-run stages. Therefore, the biomass pellets has not been fully burned, so the CO emission is high. When the combustor goes into the operation stage, the air blower runs fully, and the temperature increases, the combustion performance is stable, therefore the biomass pellets can be fully burned, so the CO emission is low. When the combustor stops, the air blower stops working, the unburned biomass pellets can not be fully burned, therefore, the CO emission goes higher.
Table 1 The CO emission concentration of eight types of biomass pellets
SO2 and NO emission during biomass pellet combustion
During the start-up, pre-run and stop stages, the SO2 emission concentration is higher, which is also caused by incomplete combustion. During the operation stage, the majority of biomass pellet shows extremely low emission concentration of SO2, which is because there are low sulphur content in biomass. But cotton stalk is an exception. The SO2 emission concentration of cotton stalk pellets are much higher than other biomass pellets, although, the sulphur content of cotton stalk is not high. This indicates that the generation mechanism of SO2 is complicated. It is not only related to the sulphur content, but also related to the biomass type and combustors type.
The NO emission concentration of eight types of biomass pellets has been placed as follow. The No emission concentration of eight types of biomass pellets are proportional to the nitrogen content of the biomass pellets. The higher the nitrogen content of the biomass pellet is, the higher NO emission concentration will be.
Table 2 The NO emission concentration of eight types of biomass pellets
The influence of ash content on combustion
There is a significant influence of the biomass pellets ash content on the operation time of the combustor. If the ash content of the biomass pellets is too high, the combustor may be hard to operate because of the discharge failure of the ash content. Cotton stalk pellets has the highest ash content, which is 21.69% of the total pellet weight, but the slagging rate is low, only 24.13%. But the operation stage of cotton stalk pellet is the shortest, only 7 minutes. Besides, the slagging rate also has strong influence on the operation time of the combustor. Take Korean pine pellet as an example, the ash content of Korean pine pellets is 6.32%, but the slagging rate of Korean pine pellet ash is 57.81%. The slagging problem may block the inspection hole of the combustor, which may stop the combustor.
Table 3 The ash content, slagging rate and running time of eight types of biomass pellets
Biomass Pellet Combustion Property Test Result
The ignition time of biomass pellets is related to the volatile content and moisture content of the biomass pellets. High volatile content and low moisture content makes the ignition time shorter.
During the combustion period, biomass pellet release contaminants such as SO2 and NO far lower than the national standards. But some biomass pellets shows problems like high ash content, or serious slagging problem, so choosing the suitable biomass pellet is very important.
The elements that mainly effect the slagging rate of the biomass pellets are silicon, alkalis and alkaline earth. High silicon content of biomass pellets means high alkalis content, which makes the ash easy to slag. But high alkaline earth content means less slags. Therefore, add proper additives can improve the slagging problem effectively.