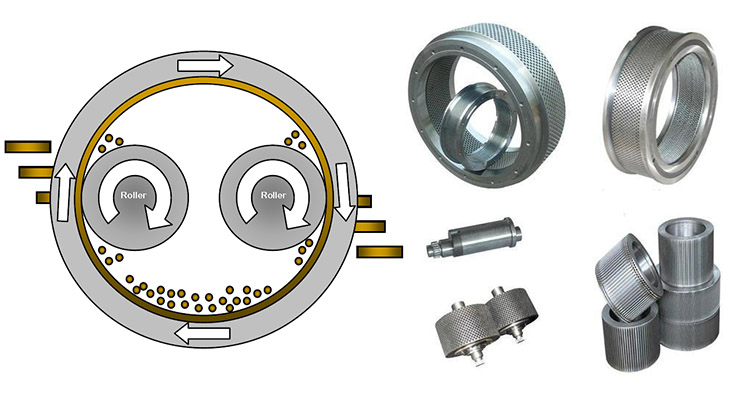
For the industrial pellet plants, ring die pellet mill is the core machine of the complete wood pellet processing line. The name “ring die pellet mill” is named after its die shape. And for a ring die pellet mill, the design of the ring die is extremely important as it is the main wear part of the ring die pellet mill. The main parameters of ring die are: the diameter of ring die, the effective width of compression, rotary speed of ring die, the diameter of rollers and the raw material of ring die.
Reasonable Parameters of Pellet Mill Ring Die
The diameter of effective width of ring die
According to the different parameters and series of preferred numbers of ring die pellet mills from both home and abroad, the suitable diameters of ring die are 250mm, 300mm, 320mm, 350mm, 400mm, 420mm, 508mm, 558mm, 678mm, 768mm. And the power for ring die pellet mills with different diameters should be 15kw, 22kw, 37kw, 55kw, 75/90kw, 90/110kw, 132/160kw, 180/200kw, 220/250kw, 280/315kw. Then we can determine the effective width of the ring die (the width of the contact segment of the ring die central part and rollers) based on the ratio of the compression area and the equal power (normally, the ratio is between 14 and 22 cm²/kw).
The rotate speed of ring die
The rotate speed of ring die is related to the geometric parameters of the ring die pellet mill. According to all the existing documents and years datawatch of the technical parameters of both domestic and foreign ring die pellet mills, the linear velocity of ring die inside radius should be 4 – 8m/s for the ring die pellet mills with two rollers. The linear velocity strongly effect the time for the raw materials passing the die holes. Therefore, it can definitely effect the pellet mill capacity and pellet quality. If the linear velocity is too high, the ring die pellet mill produce less pellets under the same production conditions. Moreover, a high linear velocity makes the material layers thinner, and dispatch the materials unevenly, so the wood pellet density is too low. If the linear velocity is too low, although it can produce wood pellet with excellent wood pellet, but the pellet mill capacity is also very low, which will strongly increase the cost of production.
The diameter of rollers
The working principle of ring die pellet mill is using the extrusion force between the ring die and the rollers to make the materials pass through the die holes, which uniformed the material into high density wood pellets. If we use the same ring die, when the diameter of the rollers increase, the compression area between the ring die and the rollers increase too.
Theoretically speaking, for the pellet mill with single roller, the larger the diameter of the roller is, the better pellet it will make. But the capacity of the single roller ring die pellet mill cannot satisfy the industrial wood pellet production. For large scale wood pellet production, the double roller ring die pellet mill shows a better performance. For the ring die pellet mill with two rollers, the ratio of the roller outer diameter and the ring die inner diameter is 0.475 based on the existing documents, and then we can determine the diameter of the rollers.
Suitable Material for Pellet Mill Ring Die
After the determination of the size of the ring die, we should focus on choosing the suitable material to make the ring die. The material properties effect the intensity, abrasion performance and corrosion resistance of ring die directly.
There are three kinds of steel which has been used as the ring die material, carbon steel, alloy steel and stainless steel. According to Chinese Steel Standard, the main carbon steel is 45 steel, its hardness during heat treatment is HRC45 – 50, its abrasion resistance and corrosion resistance is not enough for ring die. The main alloy steel is 20CrMnTi, it has been heating treated such as case carburization, so its hardness is above HRC50, and has good mechanical property. The ring die made by 20CrMnTi shows a high intensity and abrasion resistance performance, but its corrosion resistance performance is poor. Although, the cost of alloy steel ring die is lower than stainless steel ring die, but during pellet production, its poor corrosion resistance performance will decrease the working life of the ring die, you have to change the ring die frequently, which makes the actually ring die cost higher than stainless steel ring die. The main stainless steel is 4Cr13, its has good rigidity and tenacity. Its heat treatment adopts the whole heating quenching technology, the hardness is more than HRC50. Moreover, it has good abrasion resistance and corrosion resistance performance, which enhance the working life of ring dies and make 4Cr13 stainless steel the most cost effective material to make ring dies.