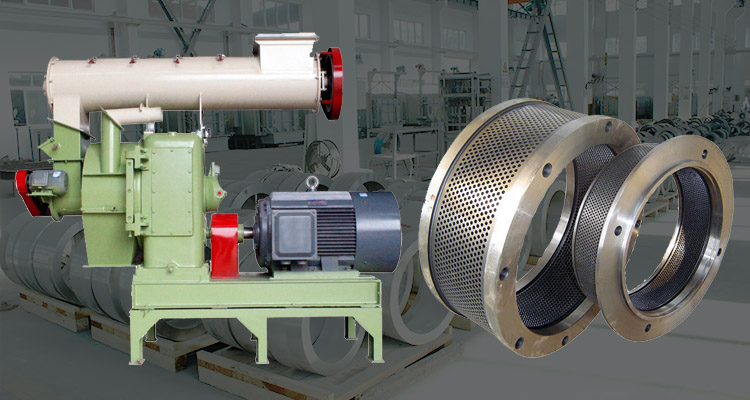
In a complete pellet production line, ring die pellet mill is the core equipment. And in a single ring die pellet mill, ring die is the core component, it is the main wearing part of a ring die pellet mill. According to the statistics, the cost of wear and tear of ring die covers more than 25% of the whole maintenance cost of the producing department. Moreover, it also effect wood pellet quality directly. Therefore, to get to know the knowledge of features of pellet mill ring die is significantly important for the pellet makers. It can help them choose suitable ring die pellet mill, use it properly and maintain it effectively.
Pellet Mill Ring Die Material And Heat Treatment
There are three kinds of steel which has been used to produce pellet mill ring dies, carbon structure steel, alloy steel, and stainless steel. After heat treatment, the rigidity of carbon structure steel is normally HRC45-50, the abrasive resistance and corrosion resistance performance are poor, which has been used to produce low-end pellet mill ring dies. The rigidity of alloy steel is over HRC50 after the heat treatment. Alloy steel has good combined mechanical properties, the pellet mill ring dies made by alloy steel has high intensity and good abrasive resistance performance. But the disadvantage of alloy steel pellet mill ring die is also severe, the alloy steel ring die has poor corrosion resistance performance. Stainless steel has excellent rigidity and tenacity, the rigidity of stainless steel is above HRC50. The abrasive resistance and corrosion resistance performance of stainless steel are also very good. Therefore, the working life of stainless steel ring die is longer than other kinds of pellet mill ring dies.
Pellet Mill Ring Die Pore Structure, Compression Ratio And Roughness
The common die hole shapes of pellet mill ring die are straight cylindrical holes, ladder shaped holes, external cone shaped holes, internal cone shaped holes and so on. The ladder shaped holes can be divided into release type ladder shaped holes (also known as pressure relief holes) and compression type ladder shaped holes. Different types of die holes are used to produce different kinds of pellet products.
The compression ratio of pellet mill ring die is the specific value of the effective length and minimum diameter of the die holes of ring die, it is a important indicator to determine the pellet mill extruding strength. The larger the compression ratio is, the stronger pellet the machine will produce.
For the compression ratio of ring die with straight cylindrical die hole, the effective length of die hole is the thickness of the ring die, the minimum diameter of die hole is the same with the diameter of the die hole. For the compression ratio of ring die with release type ladder shaped die holes and external cone shaped holes, the effective length of die hole is the thickness of the ring die minus the length of the release hole, the minimum diameter is the diameter of the smaller part of the die hole. For the compression ratio of ring die with compression type ladder shaped holes and internal cone shaped holes, we will use the ring die thickness as the effective length of the die hole, and the diameter of the smaller part of the die hole as the minimum diameter. But the compression ratio which is calculate by the above data has a different meaning compare to other ring die compression ratios.
Roughness is an important indicator of the ring die quality. Under the same compression ratio, the larger the roughness value is, the obstruction of the extrusion process is larger, which makes it harder to discharge pellets. Also, the excessive roughness will effect the quality of the surface of wood pellets. The proper roughness value is between 0.8 and 1.6.
Ring Die Working Area, Die Hole Arrangement And Ring Die Porosity
Ring die working area means the product of the perimeter of internal diameter and the effective width of the ring die.
During the drilling, the die holes are arranged circumferentially, and the neighbouring two rows of die holes must be staggered.
Ring die porosity is based on the die hole diameter and the wall thickness between two die holes. Therefore, under the same diameter of die holes, we must decrease the wall thickness between two die holes in order to increase the ring die porosity. But the minimum wall thickness must be able to endure the needs of the intensity of the ring die. The larger the diameter of die hole is, the higher porosity the ring die will get.
Ring Die Linear Velocity
Ring die linear velocity is the tangent speed of internal circle of the ring die. The value of ring die linear velocity effects the thickness of the raw materials in the press chamber and the time for the materials to pass the die holes. Therefore, it can effect the capacity of the ring die pellet mill and the wood pellet quality. If the linear velocity is too high, there may be a fault of the materials in the press chamber. So the produced wood pellets are soft and fragile. If the raw materials have higher moisture content, it may cause the breakdown of the pellet mill. If the linear velocity is too low, it can produce high quality wood pellet, but the pellet plant capacity will be extremely low, which can not match the need of industrial scale wood pellet production. The common ring die linear velocity is between 6-9m/s.