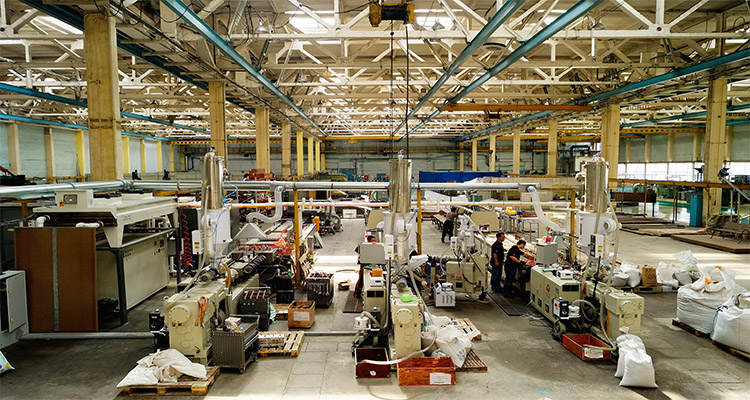
What is Pellet Plant Automation?
Theoretically, every industry will experience a period of automatic revolution. As the computer information technology is developed, the control system and even the production line of the plant are tend to be automatic.
Take wood pellet production industry as an example, for small scale wood pellet production, the pellet mill with manual control system is the standard and most popular pattern, as a result of the non-commercial wood pellet production or the limited budget. The usage of small scale wood pellet production is various, maybe it’s for their own house heating, maybe it’s for their own work shop power generation. The applications determine the priority position of the budget. On the contrary, the large scale wood pellet plant is definitely a commercial facility. Whoever the customer is , the wholesaler, the retailer, or even the power station, the large scale wood pellet production is made to be profitable. Due to its massive quantity and short production time, the manual control system lost attraction to the wood pellet plant. Therefore, the wood pellet plant automation takes place.
Pellet plant automation, aka automatic control system of pellet plant, is a system to control the operation of the whole wood pellet production line. Automation can be realized by many different ways, such as mechanical, hydraulic, pneumatic, electrical, electronic devices and computers, mostly in combination. The classic automatic control system of wood pellet plant is the PLC.
The Introduction of PLC Control System for Wood Pellet Plant
Basic structure of the PLC control system
PLC, programmable logic controller , adopts a kind of programmable memories, and use it to run a series of instructions towards the users, such like store the programs, perform logical operations, sequential control, timing, counting and arithmetical operation, etc. Then, the PLC can control the production process via digital or analog input and output. In another word, you can treat the PLC as a computer which is specialized in controlling industrial production line. The hardware structure of PLC is similar to micro computers, which include: power, CPU, memories, input and output interface circuit, function module and communication module.
Work principal of the PLC control system
The working procedure of PLC can be divided into three stages, the input sampling, the execution of user programs and the output refresh. The completion of the three phases is called a scan cycle, and during the running period, the PLC execute the scan cycle repeatedly.
During the input sampling stage, the PLC scans every input state and data in turn and store them into the corresponding units in the I/O image area. After the input sampling phase, the PLC will turn to the next two phases, but no matter how the input state and data changes, the state and data in the I/O image area won’t change. Therefore, if you are input the pulse signal, make sure that the width of the pulse signal is more than a scan cycle.
During the execution of user programs, the PLC always scan the user programs from the top down and from the left to right. Then the PLC will do the logical operation to the control circuit with the same order. According to the RLO (result of the logical operation), the corresponding state of the logic coil in the RAM memory area will be refreshed, so the PLC will determine the special instruction of the user programs will be executed or not.
After the execution of user programs, the PLC goes into the output refresh stage. During the stage, the CPU will refresh every output latch circuit based on the state and data of the corresponding units in the I/O image area, and then actuate the corresponding peripheral equipment through the output circuit.
The components of PLC control system for wood pellet plant
- The screen for the administrators to supervise the wood pellet production process flow analog.
- The PLC and the intelligent instrument
- The pellet plant alarm system
- The automatic controller of pellet mill
- The intelligent ammeter for the wood pellet mill
The Highlight of PLC Control System for Wood Pellet Plant
Convenient in operation, simple in programming
The PLC control system for wood pellet plant uses a simple programming language, for example: the ladder diagram, logic diagram and statement list. There is no need for the administrator of the pellet plant to have a computer major background. The development period of the system is short, and it is easy to debug on the field. Besides, the operation program can be revised online, there is no need to disassemble the hardware.
Competitive price
There are many different controllers on the market, the traditional electric relay, PLC, DCS, etc. Compare with the other controllers, the PLC remains a strong function that can realize some sophisticated control requirements and a lower price.
Mature hardware
The PLC products are the proven commodities on the market. It is standardize, serialize and modularize and has various hardware devices for the customers.
High reliability
The traditional relay control system uses a large amount of intermediate and time relays, as there are a lot of contact points and link points, the failure possibility is high. To improve that, PLC uses the software instead of the relays, so the link points has been reduced to about 1% – 10%. In addition, the PLC adopts a series hardware anti-jam measures and software anti-jam measures, the average MTBF (mean time between failure) is about tens of thousands of hours. By now, the PLC is recognized as one of the most reliable industrial control devices in the world.
Little maintenance work
PLC gets a low failure ratio and impeccable self-diagnosis and display system. If the PLC or the external input device and actuator is fail to operate, you can find out the reason of the failure immediately via the information provided by the programmer and clear the troubles by changing the modules.