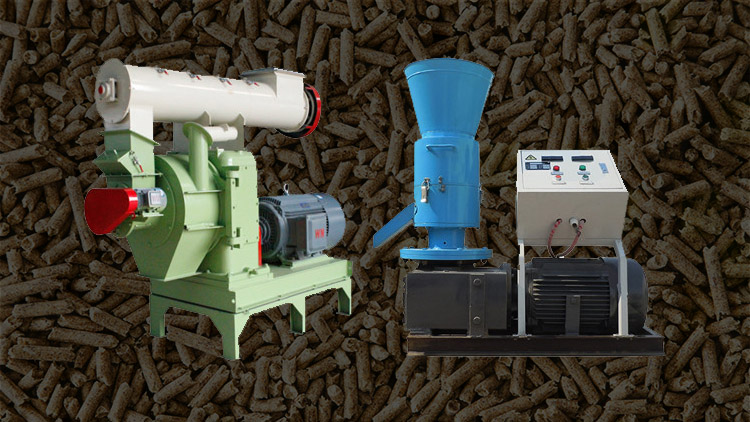
The energy and environment problem have become the key focus global wide. Due to the requirements of the rapid economic development, the contradiction between energy and environment has been more and more serious. The over-exploitation of coal makes the coal source decreases rapidly, moreover, during the mining, it causes huge damage of the environment, such as the land subsidence, the damage of headwaters area, etc. Talk about the petroleum, the oil sources are concentrated, so most of the countries’ oil demand depends on import, which makes you controlled by others, and may cause the energy crisis.
As the traditional fuel sources (coal & oil) has been decreased rapidly, the global forest industry generates millions tons of wastes and auxiliary materials such as branches, logs, straw, etc. The utilization of the auxiliary materials of the forest industry will ease the social dilemma on energy, and at the same time, it can reduce the environment problems caused by wrong process procedures. But the wood raw material has a low density, which makes the burning efficiency low and the transportation and storage cost high. So, by using the pelletizing technology, press the raw materials into wood pellet can perfectly solve the energy problem we are facing now. That is also why there are more and more wood pellet plants have been established recently.
The Way to Make Biomass Pellets
Chinese researchers began to study the biomass pelletizing technology in 1980s. When we review the history of pellet mills, there are three pellet forming types which has been used in China, the spiral extruding type, the piston ram type, and the die & roller extruding type.
As the raw materials to make biomass pellet have wide varieties, and complicated characteristics, so the requirements of the pellet production equipment is extremely high. The equipment must be anti-abrasive, highly optimized for general use, steady operation performance and high productivity. Now, the die & roller extruding type pellet machine has been wide accepted by the global biomass pellet manufacturers. There are two types of die & roller extruding type pellet machine, which has been called as the ring die pellet mill and the flat die pellet mill.
Ring Die Pellet Mill VS Flat Die Pellet Mill
Introduction of Ring Die Pellet Mill
Ring Die Pellet Mill Working Principle
The biomass materials will be fed in the press chamber through a automatic spiral feeder, and then be spread evenly between the ring die and rollers. The ring die is rotating mainly driven by the main electrical machine, and the rollers are installed in the inner side of the ring die. Therefore, the rollers can keep pressing the biomass materials through the holes on the ring die.
Ring Die Pellet Mill Features
Force feeding system: the ring die pellet mill has a much larger production capacity than the flat die pellet mill, the manual feeding system is no longer suitable for a large scale pellet production. Therefore, ring die pellet mill mainly adopts the spiral conveyor to feed the biomass materials into the press chamber.
Suitable electrical machine: the forming of biomass pellet is more difficult than the forming of feed pellet. The moisture content of the biomass materials before pelletizing must be controlled between 13% – 18%. The ring die pellet mill has a much faster rotary speed than the flat die pellet mill, so during the pelletizing process, the rotary speed of the ring die must be controlled. There must be a proper time for the biomass material to stay in the holes of the ring die to complete its forming need. During the pressing, the pressure is between 50 -100MPa, and that is why we need the high torsion low rotational speed electrical machine. Most of the ring die pellet mill use the grades 8 electrical machine, the rotate speed is about 750r/min, when the torsion enhanced, the rotate speed is about 141r/min.
High quality forging parts: all the shaft parts of Gemco ring die pellet mill are made by the high quality forgings, which will definitely add the serve life of the ring die pellet mill.
Ring Die Pellet Mill Performance
Gemco ring die pellet mill is a fully automatic pellet machine with a much larger capacity than the flat die pellet mill, normally 1 -2 ton/h. Therefore, the ring die pellet mill has been accepted by the majority of the global wood pellet plants. By connecting several ring die pellet mill together, the capacity of a wood pellet plant can reach to 20 ton/h.
Introduction of Flat Die Pellet Mill
Flat Die Pellet Mill Working Principle
The electrical machine drive the main shaft via reduction gearbox, the main shaft drives the rollers, the rollers rotate around the main shaft and also spin on their axes.
The biomass raw materials will be fed in the feed chamber manually. Under the influence of the material distributor and scraper, the biomass materials will be spread on the flat die evenly. The rollers keep pressing the biomass materials continuously, then the materials will be pressed into the die holes. Finally, the materials will be extruded out as the uniformed biomass pellet.
Flat Die Pellet Mill Features
Feeding method: flat die pellet mill adopts the manual feeding system, the biomass materials will fall into the feed chamber under gravity, and then spread on the flat die.
The placement of pellet die: the flat die has been fixed on the engine base, the biomass materials has been extruded out of the stationary flat die. The fixed flat die is good for the improvement of the pellet forming ratio.
The rollers: the rollers of flat die pellet mill has a low rotate speed, and both of the inner side and outer side of the rollers will slip during the extruding period. Objectively speaking, this type of working principle enhances the extruding performance of the pellet machine.
Flat Die Pellet Mill Performance
Gemco flat die pellet mill has a pellet forming ratio which is over 90% by using the raw materials such as wood shavings, saw dust, corn stalks and so on. The capacity is between 250 – 800kg/h.