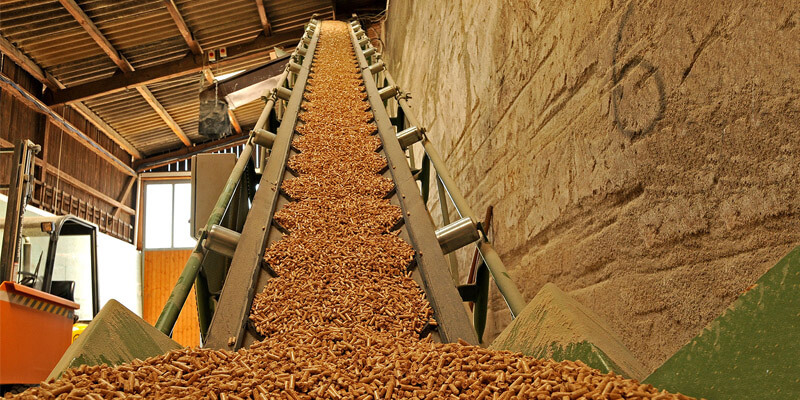
Ring die pellet mill is the core equipment of a complete wood pellet production line. The production capacity of ring die pellet mill is larger than small pellet mill, about 1ton per hour, therefore, ring die pellet mill are most used in industrial wood pellet plants.
Wood Pellet Production Process
The complete wood pellet production process can be separate as the following sections:
Raw materials collection: there are many different biomass raw materials can be used to produce wood pellets, such as crop stalks, rice husks, peanut shell, wood branches, sawdust, wood chips, etc. Before starting to produce wood pellet, there must be raw materials quantity for at least one week production in stock. And the warehouse for biomass raw materials must be rain proof and fire proof.
Raw materials crushing: during ring die pellet mill working process, the size of biomass raw materials must remain the diameter of 3-5mm. Except the sawdust, other biomass materials must be crushed and grinded before it can be fed into ring die pellet mills. Typically, wood crusher is used for the initial wood material crushing, and hammer mill is used for wood material final grinding.
Raw materials drying: ring die pellet mill has strict raw material moisture content limit, the moisture content of biomass material must be less than 18%, for the best quality wood pellet, the moisture content must be lower than 10%. If the moisture content is too high, the wood pellet may failed to form into uniformed solid fuels; If the moisture content is too low, the wood pellet may be cracked. So an industrial rotary dryer is one of the main equipment in wood pellet production line.
Raw materials conveying: manual feed method can not satisfy industrial wood pellet production. In order to save labor, pellet production lines always go with an screw conveyor that can convey the biomass material to ring die pellet mill automatically.
Pelletizing: ring die pellet mill is the core machine of the complete pellet line. When biomass materials have been fed into pellet mill chambers, pellet mill ring die and rollers extrude the materials to pass through the holes on pellet mill ring die, and outside the pellet mill ring die, there is the knife cut the discharged round biomass battens into small pellet.
Pellet cooling: the temperature of the just-made wood pellet can reach 80 or 90 degree, it is too hot to pack, and if we let the wood pellet cooling itself, it may regain moisture. So after pelletizing process, wood pellet will be conveyed into pellet coolers directly.
Pellet package: after cooling process, wood pellet will be conveyed to pellet package machine. There are normally two types of package quantity, the bulk package, and retail package. Bulk package will pack wood pellet into bags with 1ton quantity, and retail package will pack wood pellet into bags with 15kg quantity.
Ring Die Pellet Mill Wear Parts Installation Design
The most important wear parts of biomass ring die pellet mills are pellet mill ring die and rollers, the tapered roller bearings that can sustain both the radial force and the axial force. When the pellet machine manufacturers set up their axial internal clearance must take the thermal expansion into consideration.
If the pellet machine manufacturers choose to use X type distribution method, then the increasing temperature will always make the axial internal clearance decreases.
If the pellet machine manufacturers choose to use O type distribution method, then there will be three different situations:
- When the APEX (the common point on the axis of a bearing where angular lines of the tapered roller surfaces meet) overlaps, the pellet roller axial internal clearance is not influenced by the thermal expansion.
- When the distance between two tapered rollers is short, the APEX of tapered rollers are interlaced, the axial internal clearance of pellet machine bearing will decrease as the thermal expansion increased.
- When the distance between two tapered rollers is large, the APEX of tapered roller will not be interlaced, the axial internal clearance of pellet machine bearing will increase as the thermal expansion increased.
During the working period of biomass ring die pellet mill, the extrusion and friction among pellet mill ring die, rollers and wood materials generates large quantity heat, these heat definitely will cause the changes of pellet machine roller axial internal clearance. Therefore, these situations must take into consideration during ring die pellet mill designing. As the axis of pellet mill rollers is short, no matter which installation method you choose, the axial internal clearance of pellet mill rollers will decrease in heating status.