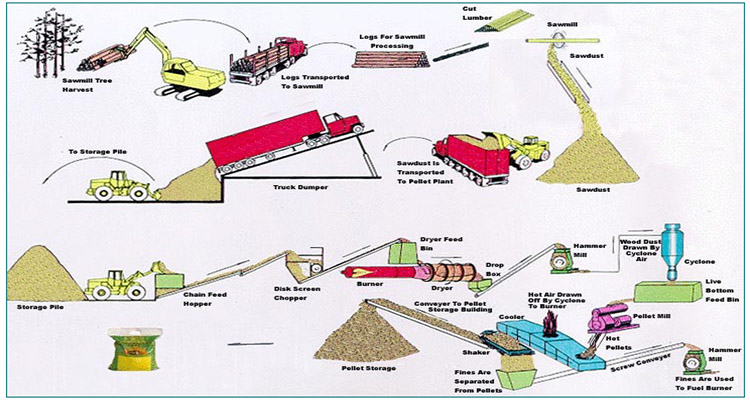
For the newcomers, to have a general idea about the wood pellet manufacture industry is one of the eager requests, such like the wood pellet plant process flow. It is easy for everyone to understand that the main equipment in pellet plant is the pellet mill which is used to mold the raw materials into wood pellet, but the whole wood pellet manufacture process requires many different treatments before and after the pelletizing process. The basic wood pellet plant process includes 8 steps, and in the rest of this article, I will try to give the beginners some detail information about each wood pellet plant process and the machines it may need.
Pellet Plant Process Instruction for Beginners
Initial size reduction
The majority of the wood pellet manufacturers adopt all sized wooden raw materials, such as the logs, barks, saw dust, wood shavings, etc, which indicates that the size reduction process is not only a necessary step for wood pellet plants, but also extremely costly. The reasons can be seen as follow: firstly, the pellet mill can only process the raw materials with a diameter less than 5mm, obviously, the unprocessed raw materials are way too big to feed in the pellet mill directly. Secondly, for the upcoming drying process, the smaller particles means a shorter drying time and lower energy requirement, and the larger particles means a longer drying time and higher energy requirement. Therefore, the initial size reduction process can help reduce the energy consumption of the pellet plant, and enhance the serve life of the other machines in the pellet plant.
The equipment we use in the primary size reduction process is normally a wood chipper, also known as the wood crusher. The knives inside the wood chipper can shred the logs or barks into small particles with a diameter less than 50mm before they can go through the next step.
For instance, be careful to avoid the foreign contaminants such like metal particles, small stone, sand, which may cause a mechanical failure or even a pellet plant safety incident.
Drying
After the initial size reduction process, the raw materials are moved to the next part, moisture reduction. Normally, the wooden raw materials has a moisture content no more than 50%, but the high quality wood pellet requires a moisture content about 8%-12%. The dryer is one of the most expensive machine in the wood pellet plant, by its obvious energy consumption. To reduce the capital input, we recommend the rotary drum dryer, which consist of a low price and simple operation procedures. In addition, the energy consumption reduction of the dryer can be realized by using the wood products in the wood pellet plant, therefore, connecting to the electric grid would not be necessary.
Due to its structure, the dryers can be divided into several types: the rotary drum dryer, suspension dryer, steam dryer, flash dryer, belt dryer, and etc. Different dryers have different features, for example, the rotary drum dryer get a competitive price, while the suspension dryer is expensive for its small footprint. The steam dryer is also very costly so only some real large- scale wood pellet plant will accept it. For flash dryer and belt dryer, the size of the raw materials must be controlled under 10mm, but the rotary drum dryer can manage a wider size range of the raw materials.
Initial sieving
For some pellet plants, the sieving procedure is not a necessary step, but in consideration of the pellet plant safety, it is a recommendable step.
After the initial size reduction process, the raw materials stay in a small particle appearance. Hence, it may easily mixed in some unpurified particles such like stone, metal pieces, which will cause the mechanical failure or even start a fire during the following steps. The machine to manage the initial sieving process would be a magnetic separator, which is an optional part for our customers.
Grinding
During the grinding process, the machine we use is hammer mill, it is also a size reduction machine. Compare with the wood chipper, the raw materials for hammer mill requires a diameter no more than 50mm, and the product it makes contains a diameter about 5mm, so that during the pelletizing procedure, the pellet mill only need to act as a molding machine not a grinding machine to enhance the serve life of the pellet mill and the lower the energy consumption. The price of a hammer mill is more expensive than the price of a wood chipper, but it maintenance costs is lower than the wood chipper.
Pelletizing
The core machine for a pellet plant is the plant mill, which used to form the raw materials into wood pellet. Actually, there are several factors that determined the choice of pellet mills for the pellet plant. Such as: the type of raw materials , the pellet plant capacity, the wood pellet quality requirement, the pellet diameter and length.
Typically, two types of pellet mills are in consideration, the flat die pellet mill and the ring die pellet mill. Both of the two types of pellet mills remain a simple working principle: the prepared raw materials will be fed into the pellet mill, and straightly go in the chamber. In it, the rollers will continually push a strong pressure to the raw materials, which will generate a higher temperature of the materials and the lignin in the wooden materials will be a natural glue for the materials. In the same time, the raw materials will try to find a way out, which is the holes on the die. So the rollers press the raw materials and force them to go through the holes in a cylinder shape. Outside the holes, there is a knife that used to cut the wood pellet into a required length. Last step, the well made wood pellet will be distributed from the discharge hole.
The most simple way to choose pellet mills for your pellet plant is to find out the capacity you need. For a household application, the flat die pellet mill is our recommendation , which has a suitable capacity, a competitive price and a small footprint. But for large scale business, the ring die pellet mill is definitely the perfect choice for you, as it maintain a large capacity and an automated procedure.
Cooling
As we have mentioned before, the pelletizing procedure will generate a higher temperature and moisture of the wood pellet, which makes the pellet very easy to deformed when it leaves the pellet mill.
In that case, after the pelletizing process, the wood pellet will be send to a cooler immediately. A cooler is used to reduce the temperature and moisture of the wood pellet and after that you can expect a dry pellet with a proper rigidity.
The types of coolers in your choice list are: the horizontal cooler, the vertical cooler and the counterflow cooler. For industrial pellet plant, the counterflow cooler is a good choice. The name of the cooler, counterflow, is mainly because the cooling air and the hot pellet are in the opposite direction, in another word, the cooler pellet contacts the cooler air, the warmer pellet contacts the warmer air, which will help keep a better quality of the wood pellet product. (Learn more about counterflow cooler).
Final sieving
After the cooling process, the main process of making wood pellet is finished. But for some commercial requirement, there might need another step, the final sieving.
During the pelletizing and cooling process, the fines is a unavoidable by-product. When you shipped the wood pellet to your customers, or wholesalers, there will be a limit of fine content. So before the storage, the finial sieving is a optional choice for wood pellet manufacturers. The different screening degrees depend on the different market conditions and specifications.
Storage
When the wood pellet reaches the storage process, it means that your wood pellet product is ready. For a large pellet plant, the storage process means an automatic bagging machine with different bagging requirements, such like: the retail bagging system that is normally used for local wholesalers, and the bulk bagging system that is normally used for industrial and oversea customers. This is not an either-or choice, one of the pellet plant we built in Australia just adopt both of the two bagging systems for their different customers.