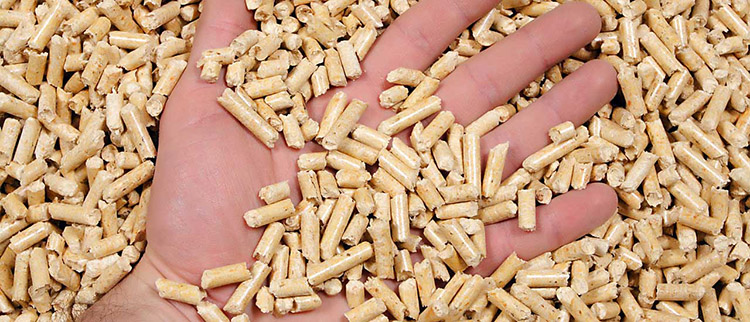
Abrasion VS Particle Density of Biomass Pellet
There are a lot of claims which is proposed by the biomass pellet plants, one of the interesting claims is about the interrelation between the abrasion of biomass pellet and particle density of biomass pellet. In 2006, an investigation has been carried out on the second World Conference on Pellets, which compared the abrasion and particle density of biomass pellets produced of the same raw materials, different fineness and with different compression channel lengths. The result shows that there are no obvious relations between abrasion and particle density of biomass pellets.
Except the relation between abrasion and particle density of biomass pellets, the investigation shows us some other elements which actually impact the abrasion of biomass pellets, such as the moisture content of biomass pellets, the utilization of biological additives containing starch. The EU project NNE5-2001-00158 reaches the similar results about the relations between the mechanical durability of biomass pellets and the particle density of biomass pellets.
Abrasion VS Moisture Content of Biomass Pellet
To find out the relations between abrasion of biomass pellets and the moisture content of biomass pellets, the investigations proposed by Elsevier has established the relations between the moisture content of biomass pellets and the abrasion of biomass pellets. The method of the investigation is to produce the biomass pellet in exact the same pellet mill of a pellet plant under the constant framework conditions, therefore, the other parameters of the biomass pellet will impact the abrasion of biomass pellet constantly. Many different tests has already confirmed that the required scope of biomass pellet moisture content is narrow when comes to the high quality pellets manufacture. The optimal moisture content of high quality biomass pellets stays between 8% and 12%, but the optimal moisture content which leads to the minimum abrasion is 12% to 13%, the higher and lower moisture content both cause more abrasion.
Abrasion VS Starch Content of Biomass Pellet
The relations between abrasion and starch content of biomass pellet is measured by a batch of pelletization trials. These pelletization trials use the spruce sawdust as the raw material of biomass pellet with the addition of maize starch. It shows a linear correlation between the abrasion and starch content of pellets, more starch content provides less abrasion.
Influence of Raw Material Storage Time
The raw materials storage time is also a strong influencer on the biomass pellet bulk density, the mechanical durability of biomass pellet, the pellet fines and the energy consumption during the biomass pellet manufacture period. The pelletization trials which use the spruce and pine as the raw materials for biomass pellet show that if we extend the storage time of the raw materials, the pellet bulk density, mechanical durability of pellet and the fines of pellet will all be impacted in a good way, only the energy consumption during the pellet manufacture period will increase as the longer storage period increased the storage input. When the storage period extend, the fatty acids and resins in the raw materials will be degraded during the storage period, therefore, the frictional forces during the pelletizing period increases which gives the biomass pellet a higher bulk density, tough mechanical durability and fewer fines. There are also some other tests show that although the concentrations of fatty acids and resins might be different, the stored raw materials are more durable and the bulk density is higher. Furthermore, it also find out that the pellet quality that used the sawdust containing a 4- 6 weeks storage period as a raw material can only be reached by using some biological additives.
The Content of Sulphur, Chlorine, Potassium and Sodium VS Corrosion Potential of Biomass Pellet
During the furnaces, the corrosion potential of biomass pellet is highly influenced by the molar ratio of sulphur and alkali compounds and chlorides in the fuel. The molar ratio equation below shows the relations between the corrosion potential of biomass pellet and the concentration of sulphur, chlorine, potassium and sodium. The corrosion potential is low when the ratio passes the value of ten. This is because the high concentration of sulphur in the flue gas will reduce the formation of alkali chlorides and increase the alkali sulphates at the same time. The alkali sulphates are more stable and less corrosive than the alkali chlorides, so the corrosion potential is lower. Last but not least, to calculate the ratio in the equation, the content of chlorine, potassium and sodium must be known. ( To find more information about the concentration of sulphur, chlorine, potassium and sodium in biomass pellet)
Gross Calorific Value of Biomass Pellet: Measured VS Calculated
The following equation is used to calculate the gross calorific value of biomass pellets. According to the equation, the content of carbon, hydrogen, sulphur, nitrogen, oxygen and ash have to be measured. All the other elements except oxygen can be analysed in a analysis programme, and then used 100 minus the total amount of the other parameters to calculate the concentration of oxygen.
But there are also some pellet plant owners who did not trust the calculated gross calorific value of biomass pellet. So some of the experts do an experiment to compare the calculated gross calorific value and the measured gross calorific value of biomass pellets. The result has be drawn as a scatter diagram which is placed below. The diagram shows a highly significant correlation between the calculated and measured gross calorific value which has a probability of error lower than 1%.
Continue your reading with other pellet plant handbook post:
Pellet Plant Handbook : The History of Pellet Mill
Pellet Plant Handbook : ENplus Certification for Wood Pellet Plant
Pellet Plant Handbook : Wood Pellet Standards in Europe
Pellet Plant Handbook : The Physical Characteristics of Wood Pellet
Pellet Plant Handbook : The Chemical Characteristics of Biomass Pellet